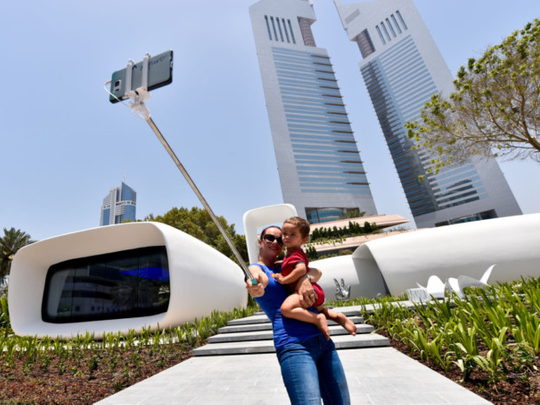
How fast can you construct a house? Well, if you can get hold of the right 3D printer, you could erect one in just 24 hours. Or rather, print it up. Earlier this year, US-based 3D-printer start up, Apis Cor, and real estate developer, PIK, announced they had successfully 3D-printed the world’s first liveable home in a day. Located in Stupino, Russia, this 38 square meter dwelling comes with a hall, a bathroom, living room, kitchen, and is stuffed with modern appliances. Apis Cor adds they are also the first to start printing houses not from the outside, but from the inside — this eliminates the need for massive printers that are typically bigger than the homes they build.
This 3D-printed house also serves as a billboard for the technology — a stated goal of the project is to convince the world that 3D printing in the construction market is now a reality. Though one market that won’t need much convincing is the UAE. 3D printers have already made inroads here, and even acquired official backing — according to the ‘Dubai 3D Printing Strategy’, quarter of all buildings in the city are to be 3D printed by 2030. The plan, unveiled in April 2016 by His Highness Shaikh Mohammad bin Rashid Al Maktoum, aims to turn the UAE into a heavyweight hub for 3D printing technologies.
No wonder Dubai is already home to the world’s first 3D-printed office building. Part of the Emirates Towers, the Office of the Future was printed in 17 days and then assembled in 48 hours. The one-storey building has a floorspace of about 250 square meters, and is the handiwork of a 20-foot by 120-foot by 40-foot printer. Speaking to international media, Mohamed Al Gergawi, United Arab Emirates Minister of Cabinet Affairs, said, “We believe this is just the beginning. The world will change.” DEWA too has joined the printer party — in September 2016, it contracted the Dubai-based construction company, Convrgnt Value Engineering, to build the world’s first 3D-printed laboratory building at the Mohammed bin Rashid Al Maktoum Solar Park. The lab will be home to research on drones and —3D printing!
On March 14, Dubai-based construction company, Cazza, also announced an ambitious plan for erecting the world’s first 3D-printed skyscraper. This unique structure will stand 1,375 feet and 80 storeys tall, joining Dubai’s skyline by 2020. An intriguing feature is that each floor will be capable of revolving independently around a central core. So if you don’t like the view, simply press a button and rotate the floor to a new one!
But for the construction industry, this skyscraper will demonstrate that 3D printers can literally rise to the occasion and go beyond low-rise structures. Cazza notes the magic here is “crane printing”, and it will help build “architecturally complex buildings at never-before seen speeds.” Apparently, the 3D printing crane can layer up to 2,153 square feet of concrete daily — that’s over 50 per cent faster than traditional methods. The technology can be tacked on to existing cranes and its initial sticker-shocker price will look a lot more palatable when the tech goes into mass production.
Apart from bragging rights for being the world’s first, 3D printing of homes and offices has substantial real-world benefits. Apis Cor notes that by hiring a printer, you save on labour costs, cut down on construction waste, and save on renting of construction equipment — “one printer can replace a whole team of construction workers, saving time without loss of quality”. The prototype house in Russia, for example, cost only around $10,000 (Dh36,730), and the printer requires just two people to operate. Similarly, the 3D printed office in Dubai worked out to around $140,000, while Al Gergawi estimates the technology has the potential to cut labour costs by 50-80 per, and reduce construction time by 50-70 per cent.
In a June 2016 study, McKinsey analysts claim the construction industry is ripe for disruption — surprisingly, productivity has declined in some markets since the 1990s, while large projects typically take 20 per cent longer to finish and are up to 80 per cent over budget. “Printing submodules or complete concrete structures before assembly could transform the industry with respect to design, cost, and time,” adds the report, while cautioning that 3D printing is still in the early stages of its development and cannot yet be deployed for large projects.
But with the UAE leading the charge, it is just a matter of time before mega projects are, well, mega-printed.